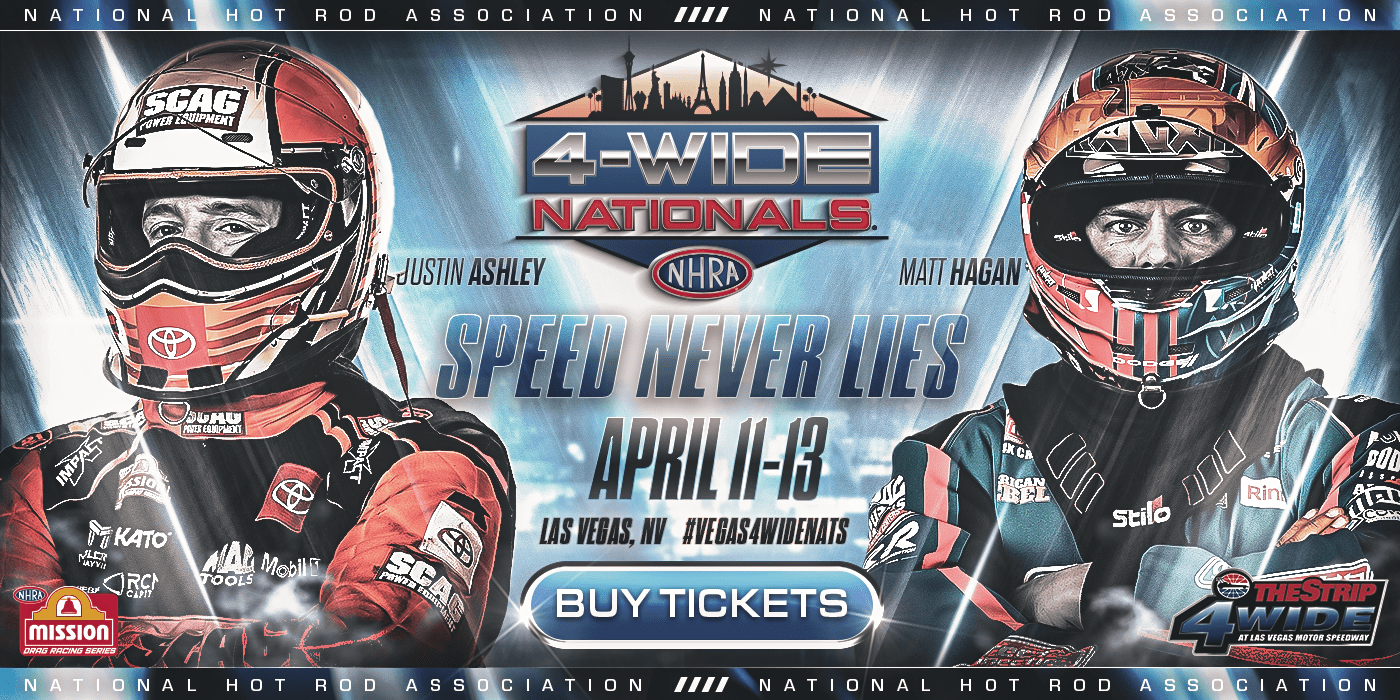
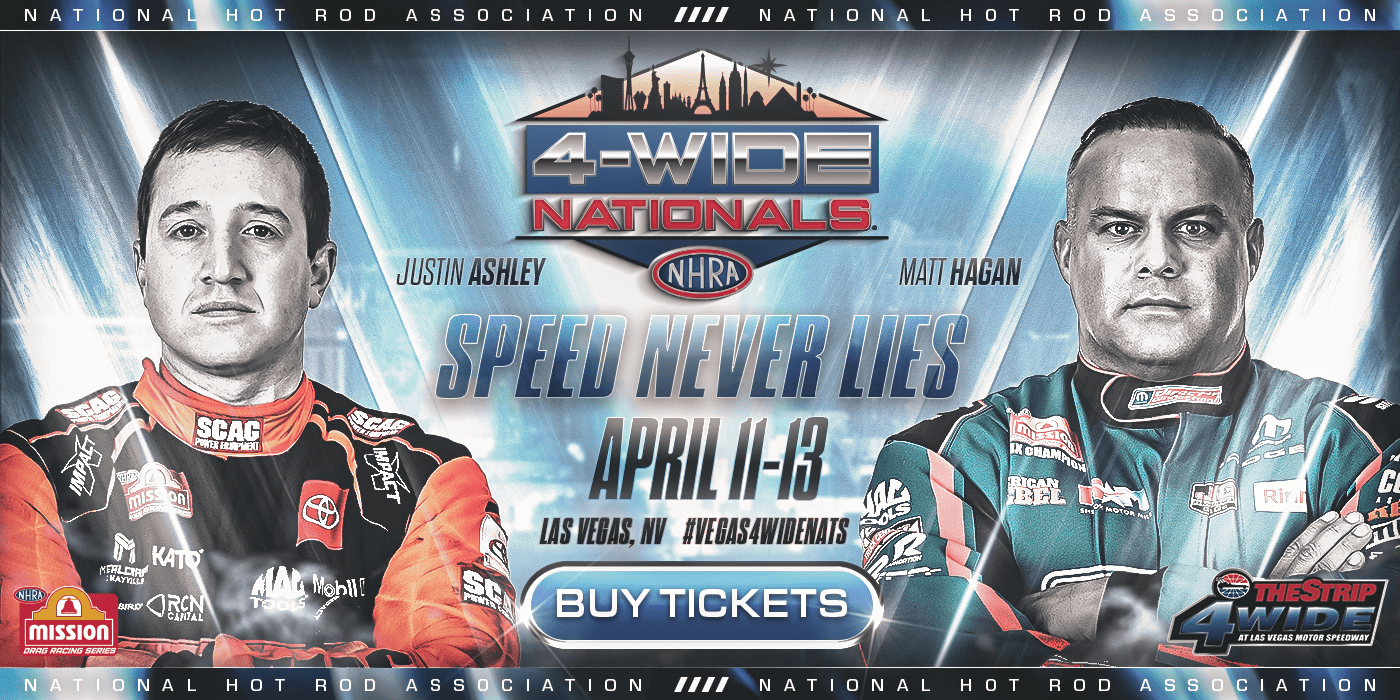
Piping for Power: How to choose the best headers for your combination
Maximizing exhaust flow is a key element in obtaining peak performance from any high-performance engine. Whether it’s a 400-hp factory muscle car on 93 octane or a Top Fueler burning nitro, a properly designed set of headers will create optimum scavenging and let the engine reach its potential.
Just like induction tuning, there’s a science to exhaust tuning. Primary pipe size and length, along with collector design (and the exhaust system, if applicable), will allow the spent gasses to flow from the cylinder heads with minimal restriction and the least amount of pumping effort from the engine.
When looking at headers, you’ll be faced with some critical options. The headers you decide upon will likely be determined by engine type, physical space under the hood, budget, and, at times, class restrictions. Thankfully, there are dozens of header manufacturers selling everything from bolt-in headers to fully custom headers designed and built for the specific needs of your engine and chassis. Additionally, you’ll need to select a header material and whether or not to use a coating.
“When choosing an optimum racing header, the primary things to consider include engine type,” said Vince Roman, owner of Burns Stainless. “We also ask, is the engine in-line or V-type? And what’s the application? Obviously, we are talking drag race engines, but more importantly, what rpm do you use to leave the line and shift, and what rpm will the engine reach when it crosses the finish line?”
He continued, “The exhaust header design will very much depend on the rpm band that the motor will be running. Also, what improvements are you after? Do you want to improve the bottom end, do you need to turn more rpm at the top? The rpm band of the engine will play an important role in determining the primary size and length of the exhaust primaries. Also, consider the cylinder head. Different cylinder heads have different mounting bolt designs and port sizes. It’s typically OK for an exhaust primary to be larger than the exhaust port — but any obstruction, such as from too small a primary tube or mismatched port/exhaust.”
Steven Zimmerman, of Stainless Header Mfg. Inc., added, “A few things to consider are whether or not anything off-the-shelf will truly perform at the necessary level or if a custom-built set would be better suited to match each racer’s unique engine configuration. And design considerations should consider primary tube size, material type, and collector merge diameter. After that, begin working toward other aspects/variables, including primary length, merge size versus exit size, step sizing, and, finally, collector or megaphone length.”
Sizing the primary tubes correctly is a great place to start. Getting this right will create the maximum power and the most useable powerband. This is where vehicle weight, transmission type, and gearing come into play. For instance, a 350 Chevy in a lightweight stick shift stocker will likely be launched at a high rpm, and the engine will never see the low side of the powerband. In this case, you may opt for a larger header that provides maximum horsepower at peak rpm without worrying about any loss of torque down low. In contrast, the same engine in a heavier automatic stocker, say a station wagon, may require a smaller primary and even an X-pipe added to the headers to increase torque at low rpm.
“Primary size and collector diameter are largely dependent on engine cubic inch, number of cylinders, peak rpm/operating rpm, but most importantly, horsepower levels,” explained Zimmerman. “Horsepower is a direct result of airflow through the engine, and thus, the greater the horsepower level, the greater demand for airflow. Of course, other aspects will drastically alter the sizing, particularly power adders, such as turbochargers, blowers, or nitrous. On top of this, there are many great software programs that can run a myriad of equations and algorithms to help determine header sizing, on top of many other features. Those programs are great for us to have, as we deal with header design every day, but for any fabricator building a one-off set, the expense of a software program may not be worth it. That’s why we offer free tech and design advice 40 hours a week for anyone who calls, whether they are purchasing from us or not. We have the experience and information to help any builder.”
We also asked: How should a racer determine if step headers are needed? Zimmerman continued, “Stepped-header designs are typically reserved for nitrous and naturally aspirated engines, although we do see a select few on blower setups. Stepped headers give the benefit of a higher velocity exhaust gas at the cylinder through a smaller tube ID, while allowing the benefits of higher flow capabilities further downstream on the larger tube ID. This is great for the driver, as the exhaust is still expanding from heat and combustion, while within the exhaust tubes, it’s dictating a larger volume of space to maintain proper flow. It’s also beneficial for the fabricator, as it allows for slip-joints and consequential lap welds on the header tubes, which can often lead to easier welds and stronger joints on the header tubes. Another beneficial effect of the stepped design is the anti-reversion property of the tubes. Having the step in the tubes will create small overlap and pressure differential, ensuring the exhaust continues to move downstream, and prevent reversion back toward the exhaust ports.
“However, that being said, a stepped-header design is not always 100% beneficial. There is always going to be extra cost associated, and any engine that operates within a narrow bandwidth of power may not see some of the benefits that a wider powerband engine may see. On top of this, the larger tubes, by nature, take up more space in an engine bay, which can be a packaging nightmare in compact applications. It can also be detrimental to boosted applications, particularly turbo setups, as it robs some of the exhaust velocity, causing an increase in turbo lag.
“Furthermore, selecting between a two-step and three-step header can largely be a matter of packaging as well as performance. To really see a benefit from each individual step, certain lengths will be required. And if a builder only has room for a 20-inch long header tube for instance, a 33/33/33 split in primary tube length will leave each primary step less than 7 inches long, which may not prove as beneficial as a two-step system split 50/50, where each tube has 10 inches of length. Granted, these are all very situational and engine-dependent variables, and it is best to discuss some of those items when more engine information is available, such as cam specs, bore/stroke ratios, and fuel types are often necessary factors as well.”
Mark Emerson, of Hooker Headers, added, “The best way to determine the optimum primary tube and collector size is at the track to note what that specific combination likes the best. That’s not always the most cost effective, so tools like Pipemax software allow users to enter their specific information to receive recommendations for the best sizes for their setup.” And as we know, there’s nothing quite like a good back-to-back track test.
Roman suggested that racers, “Come to the Burns Stainless website and fill out the race engine spec form. Burns will help racers select primary size and length headers after determining bore, stroke, compression ratio, inlet and exhaust valve sizes, camshaft design, and engine-operating rpm range. The engine rpm band is the most significant factor in determining primary length, while displacement and power are important to determine primary tube diameter.
“In addition, merge collector sizing and design is determined based on application, power output, and operating rpm range. Typically, drag racing applications without mufflers benefit from using a reverse cone-megaphone collector. The sizing of the collector outlet [or throat] and outlet diameters are calculated by application. Burns Stainless uses proprietary X-Design software to size headers and collectors. Collector sizing is based upon the engine parameters, such as bore, stroke, valve sizing, and camshaft design. The number of steps is determined based on the collector sizing and exhaust port size. A well-developed modern racing engine will normally want a three-step design. Lower output engines will want two-step, or maybe only one-step, designs.”
Remaining on the topic of design, we asked, how important is it to have equal-length primary tubes? Emerson stated, “The closer in length the primary tubes are, the better you can time the point at which they enter the collector to maintain the maximum scavenging effect for the following pulse traveling through the header.”
“This is a very controversial topic in the header industry,” added Zimmerman. “There is rarely an instance in my experience where equal-length headers are going to negatively affect performance. However, that does not mean they will always be beneficial. Equal-length headers seem to have the greatest effect in higher rpm N/A [naturally aspirated] engines and rpm-sensitive turbocharged builds. This comes into a whole world of math and theory involving both pulse-wave propagation and fluid mechanics. Things also vary greatly in the cost/benefit ratio when changing fuel types or drastically increasing primary tube lengths to match the lengths. Some builds may benefit so slightly from the equal length that it isn’t worth the cost of the fabricator’s time or the sacrifice in engine bay space for the minimal gains. In our experience, header design and building run in a hierarchy of importance beginning with primary tube size, followed by collector merge size, necessity of stepped headers or single-tube size, and then finally followed up with equal-length tubes. We certainly believe equal-length headers have their place in the performance world, and that can be proven by thousands of racers and fabricators across the world, but we also wouldn’t live or die by that design. It is largely an engine-dependent solution and certainly isn’t the most important factor in designing or building a custom header.”
Continuing on, Zimmerman stated, “Primary tube size, stepped size [if building a stepped header], and collector sizing are higher priority factors than primary length. But, assuming you have dialed in those other factors, tube length would certainly be the next best variable. Without getting too complicated, tube length will be determined on operating engine rpm or peak horsepower rpm, overall engine displacement, peak horsepower, fuel type, and then the application of the vehicle itself. A small-block crate motor with a Tri-Y setup on an oval dirt-track car will have greatly varying demands of header length than the same small-block being used in an endurance race car. There are several excellent programs out there that can give great estimations in primary pipe length based on a variety of engine and camshaft parameters. Of course, the true test will always be a dyno-tune and quarter-mile run. Noting changes in your 60-foot, top speed, and e.t. are most important. As a very general rule of thumb [N/A, most specifically], shorter tube headers are better for high-rpm applications, while longer tube headers are typically better for lower end torque numbers. Turbo systems, on the other hand, typically benefit from shorter tube length, as this decreases spool time and increases exhaust velocity relative to a longer header tube of the same diameter.
“However, sometimes, it can be more indirect in tube sizing than a builder may initially think. Generally, tube sizing is based upon horsepower, which is a direct result of airflow as determined by rpm and engine volumetric efficiency [VE]. So yes, rpm will have an effect on the best tube size to use. Higher rpm engines will usually react better with a shorter primary tube length header than a lower rpm engine. This is a result of overall exhaust flow and the pressure waves. Higher rpm engines have a higher frequency of exhaust pulses due to the exhaust valve opening/closing at a higher rate than lower rpm systems. As these pulses reverberate through the exhaust system, they can begin to interfere, causing turbulence in the tubes the longer the exhaust is contained before exiting to atmosphere.
“This is also the exact reasoning lower rpm engines perform well with longer primary tubes. The lower rate of exhaust pulses means the exhaust needs more length to lower the amplitude of the pulses and help lower the amount of radically turbulent fluid motion in the system [true laminar flow will probably never exist in an exhaust system, but the lesser the turbulence, the easier the exhaust can exit the system]. This integration of exhaust pulses is what helps improve low-end torque in a long tube header, as the engine has to use less effort in forcing out exhaust and can utilize more of the combustion forces to produce more efficient power.”
Collectors
As you can imagine, there is no “best” style/type of header collector. “Theoretically, V-8s will usually respond best to well-optimized Tri-Y designs,” said Roman. “However, Tri-Y designs must be optimized for the type of racing and engine design and often require considerable testing and optimization, whereas four-into-one designs with merge collectors can be optimally configured using X-Design and normally yield the best results out of the box.”
Zimmerman added, “Every engine application will have its own ‘best’ style of collector. N/A applications, for instance, will greatly benefit from a true merge collector, where there is a merge, of say, 3.5 inches and a conical expansion out to either a 4- or 4.5-inch collector. This ‘pinch’ at the merge point acts as a Venturi, creating a low-pressure zone inside the collector. This pressure drop causes an increase in exhaust velocity, and coupled with the four tubes all meeting simultaneously, this greatly improves scavenging of the cylinders.
Emerson added, “The type of collector you select depends on the combination, but we prefer the four-into-one merge style collector with the addition of a merge spear. The ‘four-one-style’ collector allows for a shorter overall collector if needed, and the merge spear helps smooth out the transition of the exhaust pulse entering the collector to maintain pulse velocity.”
Header Material and Coatings
There are a few different materials commonly used when building headers, and they can affect performance and durability. In simple terms, this is one area where you definitely get what you pay for.
“The most common materials used in racing headers are mild steel and stainless steel,” said Roman. “Inconel and titanium are also used, though we do not recommend titanium for most automotive drag race applications. Mild steel is the least expensive option and the most readily available. The downside of mild steel is corrosion. Not only does this limit the longevity of a header, for extreme engines with large overlap cams, iron oxide particles from the rusting headers can be ingested into the cylinder during periods of reversion, causing cylinder wall and ring damage. Corrosion can be minimized using ceramic coatings. We recommend coating the inside and outside of an exhaust header.
“There are three common stainless steels used in headers. Of them, 409 is the least expensive stainless alloy. It is a ferritic alloy containing chromium and nickel, but with relatively high iron content, making it susceptible to rust. It is better than aluminized steel but will eventually rust and also has limited high-temperature capabilities. Next is 304 stainless steel, which is the workhorse stainless alloy. It is an austenitic material with low iron content, which provides it with excellent corrosion properties. Note that 304 stainless has excellent weldability and formability, making it an excellent choice for exhaust headers. An easy way to tell the difference between 409 and 304, or other austenitic stainless steels, is with a magnet. A magnet will not stick to 304.
“The next common stainless alloy used in exhaust is 321 stainless steel. This is essentially 304 that is stabilized with small amounts of titanium or niobium, providing better strength at higher temperatures. Burns Stainless recommends using 321SS when exhaust temperatures exceed 1,400 degrees Fahrenheit, which can easily be reached in many turbocharged applications. Also, 321 may be a good choice for thin-walled headers to provide an extra margin of safety.”
He continued, “The best material for race headers are Inconel alloys. These high-nickel/chromium alloys have been used in Formula One racing for decades. The most common alloy is 625, which has excellent high-temperature properties and is recommended for exhaust, which will experience exhaust gas temperatures in excess of 1,800 degrees Fahrenheit.”
Along with material, every racer should consider a header coating. According to Roman, “Ceramic header coatings have two main purposes: They keep the exhaust energy in the exhaust tube, helping to scavenge the combustion chamber, and they assist in managing under-hood heat, protecting electronics and other sensitive components.”
Source Box:
Burns Stainless
949.631.5120
Burnsstainless.com
Hooker Headers
1.866.464.6553
Holley.com/brands/hooker
Lemons Headers
805.239.8998
Lemonsheaders.com
Pro Fabrication Headers and Exhaust
704.795.7563
Profabrication.com
Stainless Headers Mfg. Inc.
800.290.3920
Stainlessheaders.com
TA Performance
480.922.6807
Taperformance.com